COVID-19 & PPE Medical Wear: The Changing Dynamics of PPE Distribution + 6 Procurement Tips
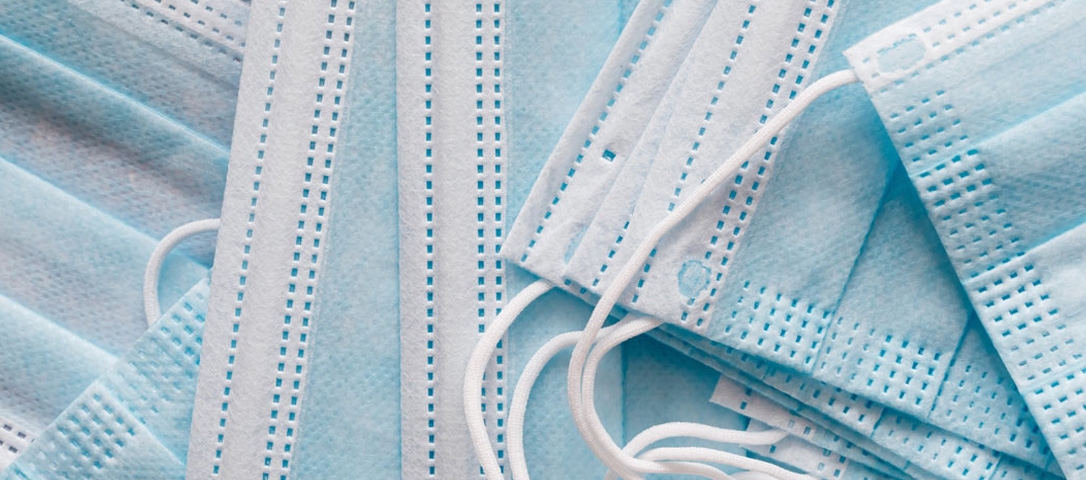
Contents Overview
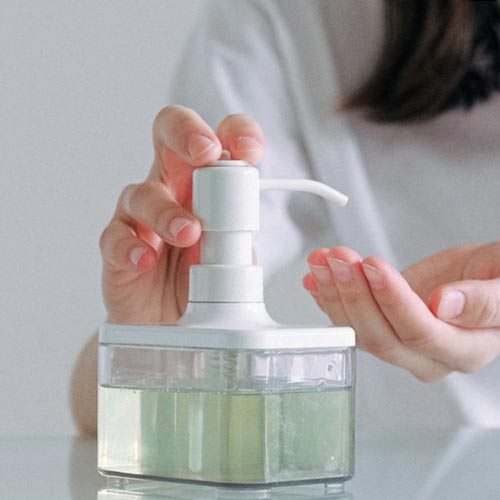
Since its first outbreak in December 2019, the Covid-19 pandemic has devastated the world. Besides testing both the preparedness and will of individuals and governments alike, the outbreak has also tested manufacturing industries with pharmaceutical and PPE manufacturers hit with the highest rise in demand. The supply chain has been challenged unlike any time since World War II. Further exacerbating this reality is the fact that government healthcare agencies and supranational organizations worldwide have been adopting “just enough” approaches over the last few decades. This means stock supplies of PPE in many hospitals have not been sufficient even before the first wave of the crisis. However, the tide has turned and now the excess capacity of equipment needed the most to fight infections is not seen as an unnecessary expense. Unfortunately, many involved in managing the crisis do not have surge capacities – the ability to manage a sudden, unexpected increase in patient volume that exceeds available capacities.
Resulting from all of this is the growing international concern regarding the shortage in the supply chain of personal protective equipment, also known as PPE. The WHO estimated that the organization would need to ship a minimum of 100 million medical masks and gloves, 25 million N95 respirators, gowns and face-shields, and 2.5 million diagnostic tests each month to meet the demand of its partners.
For example, the UN has delivered over 6.4 million gloves, 1.8 million surgical masks, and 1 million gowns to countries across the world in Q1 of 2020 only. Still, an enormous gap remains. Likewise, UNICEF estimates that needs through the end of the year could reach 2.2 billion surgical masks, 1.1 billion gloves, 13 million goggles, and 8.8 million face shields.
Therefore, manufacturers are ramping up production like never before to respond to the coronavirus crisis. This has resulted in significant price increases, making the challenge to ensure critical PPE products, not only including basic masks and gloves, but also a wide range of necessary protective medical wear, are distributed to frontline workers in all affected countries.
The fact China is one of the world’s largest producers of PPE, making the supply chain intensively one-sided, and concentrated on one area of the world, creates even bigger problems, exposing the shortcomings of globalization. The unfortunate reality is that most countries are unable to produce sufficient supplies of essential goods, such as medicine and food, to its citizens.
Intro to PPE Distribution
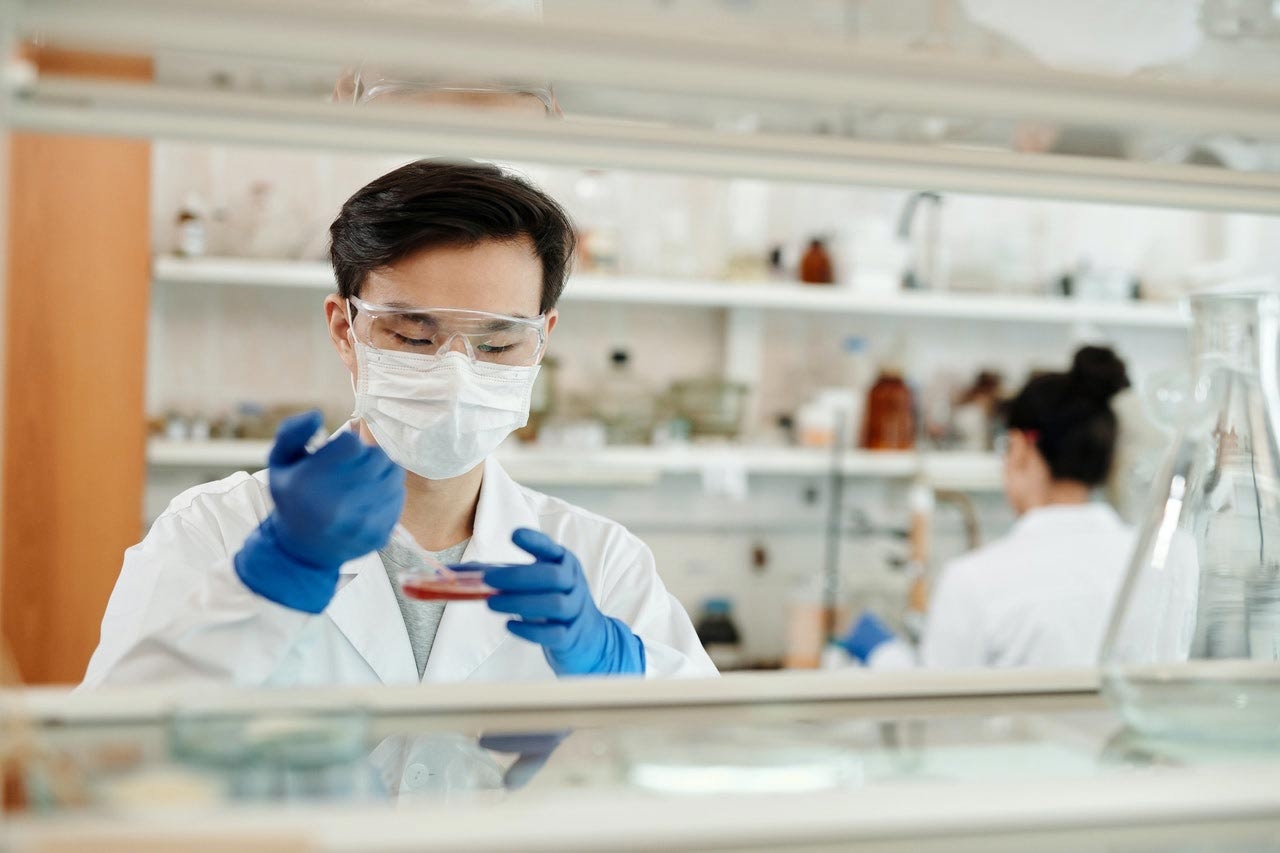
Personal protective equipment or shortly PPE is medical wear that is used every day by health care workers for protection against infections. Moreover, PPE ensures protection also for patients and other people medical professionals are providing the care for. Besides infections, like the novel coronavirus, it also protects against toxic medications or other potentially dangerous substances that are used in the healthcare industry. PPE includes gloves, aprons, isolation and surgical gowns, goggles, fluid-repellent surgical masks, face visor, protective medical clothing, respirator masks such as N95, FFP2 and KN95 masks. It is always recommended for a healthcare worker to wear at least some pieces of the protection, and even more so when there is a risk of contact with blood, body fluids, secretions, and excretions. It also protects the wearer from unnecessary injuries or the spread of infection. Raw materials required for the production of these products, usually being cotton fiber, polyester, and polyamide, are usually outsourced to low-cost suppliers.
In 2018, the global market for PPE, and only in the health sector, was estimated to be worth $2.5 billion USD. The highest revenues come from gloves (25%), followed by different suit or coveralls pieces (22%), and face masks (14%). By region, the US had the largest market share (33%), followed by Asia and the Pacific (28%), and Europe (22%) Mordor Intelligence 2020 reported for 2018.
Besides healthcare, PPE is also used in other industries. Items such as safety helmets, hazmat suits, safety footwear, safety harnesses, earplugs, ear defenders, and respiratory protective equipment are often used in factories or professions like civil engineering, especially for construction workers.
The world has jumped on overstocking the PPE supplies, and shortages are leaving many at high risks of exposure
In the hierarchy of risk control, PPE is considered to rank lowest and represent the option of last resort. It is only appropriate where the hazard in question cannot be totally removed or controlled in such a way that harm is unlikely. As this is obviously specifically true for the pandemic of a virus, the world has jumped on stocking or even overstocking the PPE supplies, and shortages are leaving many doctors, nurses, and other frontline workers of the crisis at high risks of exposure and contamination.
Supply Chain Challenges
Abrupt Disruptions, Globalization Shortcomings & the Fight for PPE Supply
It is obvious that well running medical supply chains are essential for a well-functioning healthcare system. In most parts of the world, the system was running rather smoothly, but then the pandemic hit. Supplies of once easily found PPE products on the market became scarce, and to make it even more troublesome, the demand increased significantly on the verge of fighting the novel coronavirus.
The sector was hit hard and right at the beginning because suppliers from China make up the largest share of the market. Some estimate the percentage could go up to 80-90% of the global production capacity. Lockdowns in the country resulted in lowered manufacturing capabilities, and, at the beginning of the pandemic, when Chinese people were at the epicenter of infections, once the biggest producer of PPE had to rely on other nation’s help with the supplies.
Later on, came distribution problems, and even if China quickly enabled factories to start manufacturing PPE products at the highest capacity levels in the midst of their pandemic crisis, other nations faced problems with supply transport. Mostly, because many borders were closed, and customs regulations tightened so the global network faced unprecedented problems due to an overwhelmed system. It is true some airlines stepped up by repurposing their civilian airlines to carry cargo with PPE, and some governments, like UAE, speeded up the costumes clearance processes for essential goods, such as PPE and medicines. But although actions like this helped, they did not prevent the supply chain congestion. Countries all around the world were and some still are, facing shortages of different pieces of necessary medical wear. The UK, for example, reported critical shortages of gowns. Already in March, when the Western world was only starting to enter into the pandemic, WHO Director-General emphasized that “supplies of PPE, such as the gloves, medical masks, respirators, goggles, face shields, gowns, and aprons used by health workers fighting coronavirus are rapidly depleting,” and warned against hoarding and misuse.
Another big problem is the price increase. Surgical masks, for example, saw a sixfold increase, while respirators have tripled and gowns have doubled, according to the WHO data. To make things even more complicated even exports of some raw materials that have also been running short in many places, were banned for some countries. This includes Bangladesh, Canada, Czech Republic, Egypt, France, Germany, India, Indonesia, Japan, Iran, Jordan, Kazakhstan, Kenya, Malaysia, Pakistan, Poland, China, Russia, Korea, Thailand, and Ukraine (information for March 2020). This happened for N95 masks key components – non-woven polypropylene. Learn more about supply chain disruption in the midst of the pandemic in our article.
The Big Players
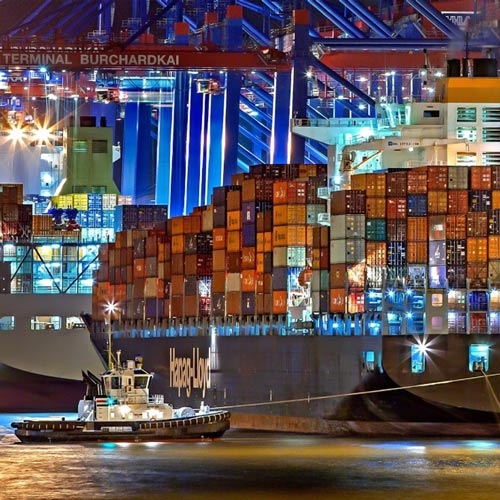
Countries and International Organizations Respond to the Crisis
No matter the supply chain challenges, there was no lack of efforts worldwide to overcome them. How did big companies and international organizations respond to a particular crisis? What actions did WHO, The Global Fund, and alike take, to help the people around the world? How did some of the biggest governments secure PPE supply for its nations?
The WHO and UN responded by setting up a Supply Chain Task Force to establish Covid-19 Supply Chain System or CSCS. The aim of the body is to bring clarity to the process of requesting and receiving globally sourced Covid-19 critical supplies, ensure a humanitarian response to the pandemic, and help national authorities and their partners request the products for their markets.
On country levels, many are implementing measures to help companies expand their production capacities. For example, in China, the government introduced support to face masks manufacturers by helping with their purchases of raw materials and hiring new workers. Additionally, they will offer tax breaks as another incentive for the factories to work at their full capacities during this critical time. Even some automobile companies, for example, have been asked to produce PPE. Similar request was made to the vehicle production industry in the US. In Japan, the government provided support for companies to increase capital investment in mask production, while securing a supply of over 600 million masks per month, and even the WHO’s director, Theodoros Adhanom Ghebreyesus, has called on governments to increase domestic manufacturing of PPE by 40%.
The WHO's director, Theodoros Adhanom Ghebreyesus, has called on governments to increase domestic manufacturing of PPE by 40%
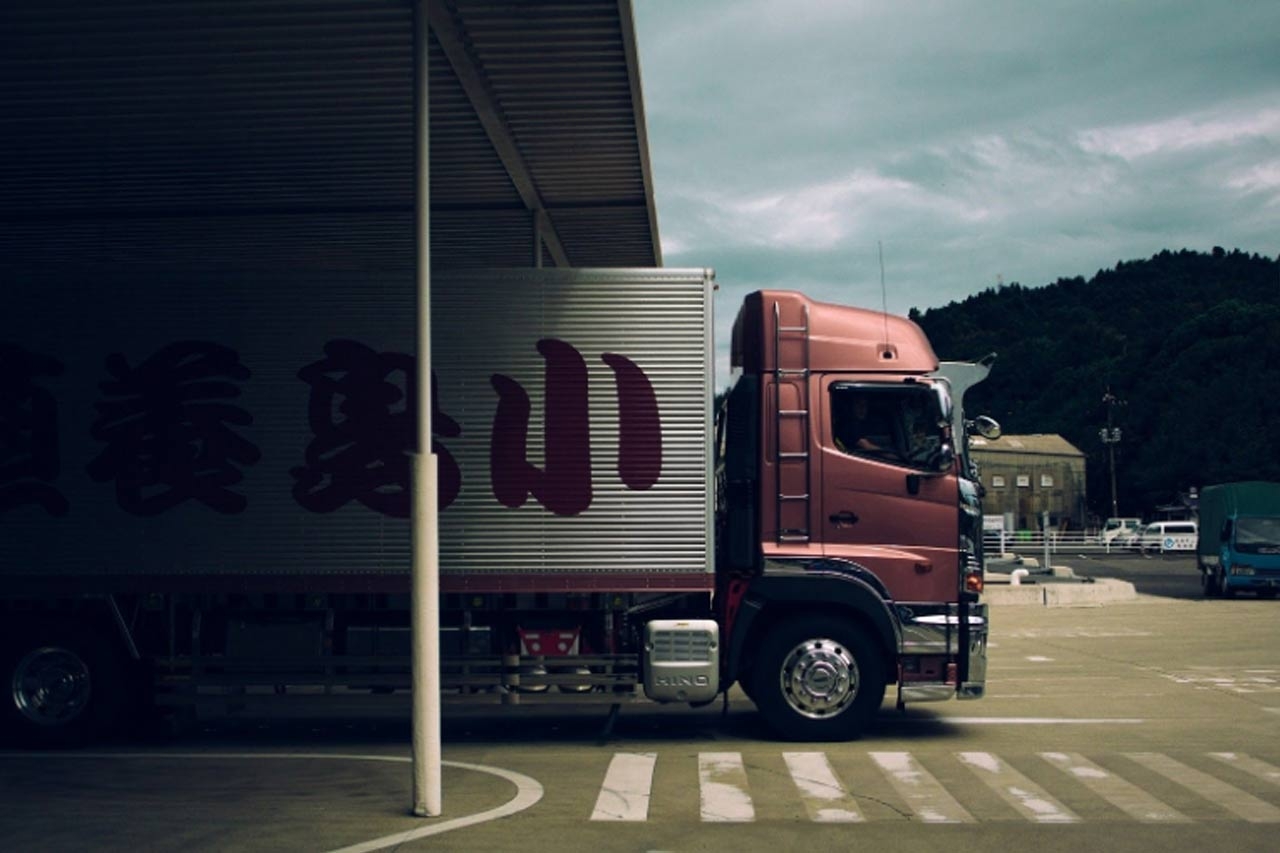
On the NGO side, project HOPE mobilized one of the first shipments of personal protective equipment to Wuhan, when the pandemic first emerged. Nowadays, The Global Fund assesses the PPE situation daily and is a good resource for updates on its supply chain. As of June 2020, for example, 11% of orders face delays of more than thirty days, including 19% of orders already in transit. The information can serve well to distributors to better develop contingency plans and plan their delivery times.
Many banks have stepped up too. Asian Development Bank has, for example, committed to providing more than $6.8 billion, including an initial support package of $6.5 billion for sovereign and nonsovereign operations while more resources are expected to be mobilized. Even more, an $800-million increase in their Trade Finance Program has already been implemented.
Finally, young companies did also not sleep through the pandemic. Many start-ups saw the opportunity to innovate and act with social responsibility in mind. One key player in logistics improvements in Nigeria was, for example, the country’s start-up Kobo360. The company uses electronic platforms to connect drivers with cargo companies to make transport of goods across the country more efficient and transparent. The company officials claim that the system can significantly reduce the traveling time of the cargo. Similarly, in Indonesia, a company called Kargo Technologies is doing the same, as it aims for regional supply chains to remain intact even in the times of crisis. As a response to Covid-19, the company also implemented an electronic proof mechanism to minimize person-to-person contact in the chain.
Distributor Guidelines
6 PPE Procurement Tips for the Coming Era
Covid-19 pandemic has brought troubled waters to the supply of PPE. However, some good can still come from it. There are many lessons that can be learned from the challenges distributors have been facing ever since December 2019.
Short-term disruptions can, firstly, result in a supply chain of PPE moving from China and India to more local industries, either in other emerging markets or even home markets of many countries as many countries are now realizing the benefits of self-sufficiency in the field of medical wear. On the alternative side, many governments are also considering more stockpiling, contingency planning, and better stock management in the country's public reserves.
Covid-19 pandemic has brought troubled waters to the supply of PPE, however some good can still come from it
Moreover, one of the biggest is the lack of innovation in the field. There has not been enough literature or research published on the reprocessing of PPE, as they have always been considered a single-use product. More work on options of sterilizations and repurposing of the equipment should follow. This would not only bring more security to any contingency plans for possible higher demands of the PPE products in future pandemic events but would also offer greater resource utilization and sustainability.
Nonetheless, all these solutions will have to be done on a larger industry-based scale. Yet, even a smaller local distributor can follow some guidelines to overcome obstacles of the pandemic era. Here are some tips from AdvaCare’s Sales team experts on procurement and supply process of PPE:
ENSURE WITH VENDOR THAT PRODUCTS ARE LAWFULLY APPROVED FOR EXPORT
Most of PPE products get sourced from China, so it is good you get familiar with current applicable export regulations. Make sure you get updates regularly as in the pandemic times situations are changing daily. As of now China’s PPE’s are classified with 7 categories: Coronavirus Testing Kit, Medical Protective Outfits, Ventilators, Medical Protective Masks, Surgical Masks, Disposable Medical Masks, Infrared Thermometers. When working with AdvaCare you can always rely on the Sales Associate assigned to your account for the updates.ENSURE TO COMPLY WITH IMPORT RULES
Keep in mind every country has different technical specification requirements for PPE imports. Even if the pandemic has hit us on a big scale and some guidelines were made by WHO on a global level, it is always good to check your destination country rules and regulations. After doing this, be sure to inform your Sales Associate about it.PPE DEMAND IS HERE TO STAY, PLAN ACCORDINGLY
It is forecasted the demand for PPE will only grow in the near future. Even before the pandemic, the industry had a projected growth at a CAGR of 6.5% from 2017 to 2022. It is only logical, the coronavirus crisis will only speed up the process. However, pricing dynamics, changes in the competitive landscape, and demand-supply imbalance for masks, respirators, and gowns in severely affected countries will influence how the market develops. Make sure to plan ahead and inform your PPE providers, such as AdvaCare, about your future order plans.IF CONSIDERING ALTERNATE PPE, CAREFULLY ASSESS QUALITY AND LOCAL MARKET PREFERENCES
In the time of excessive needs of PPE, the market has been scarce with specific types of PPE that can be provided when making your order. It is not uncommon to think of alternatives and try to help out your community with other types of protection, especially for non-essential personnel or individuals. In the end, it is better one protect oneself with something rather than nothing. However, before ordering, keep your final customer in mind. What do they do? What do they need protection for the most? When having those answers, be sure to check if the PPE offered will offer benefits and not the opposite – increase overall risks. Further advice may be sought from your supplier of PPE, such as AdvaCare.
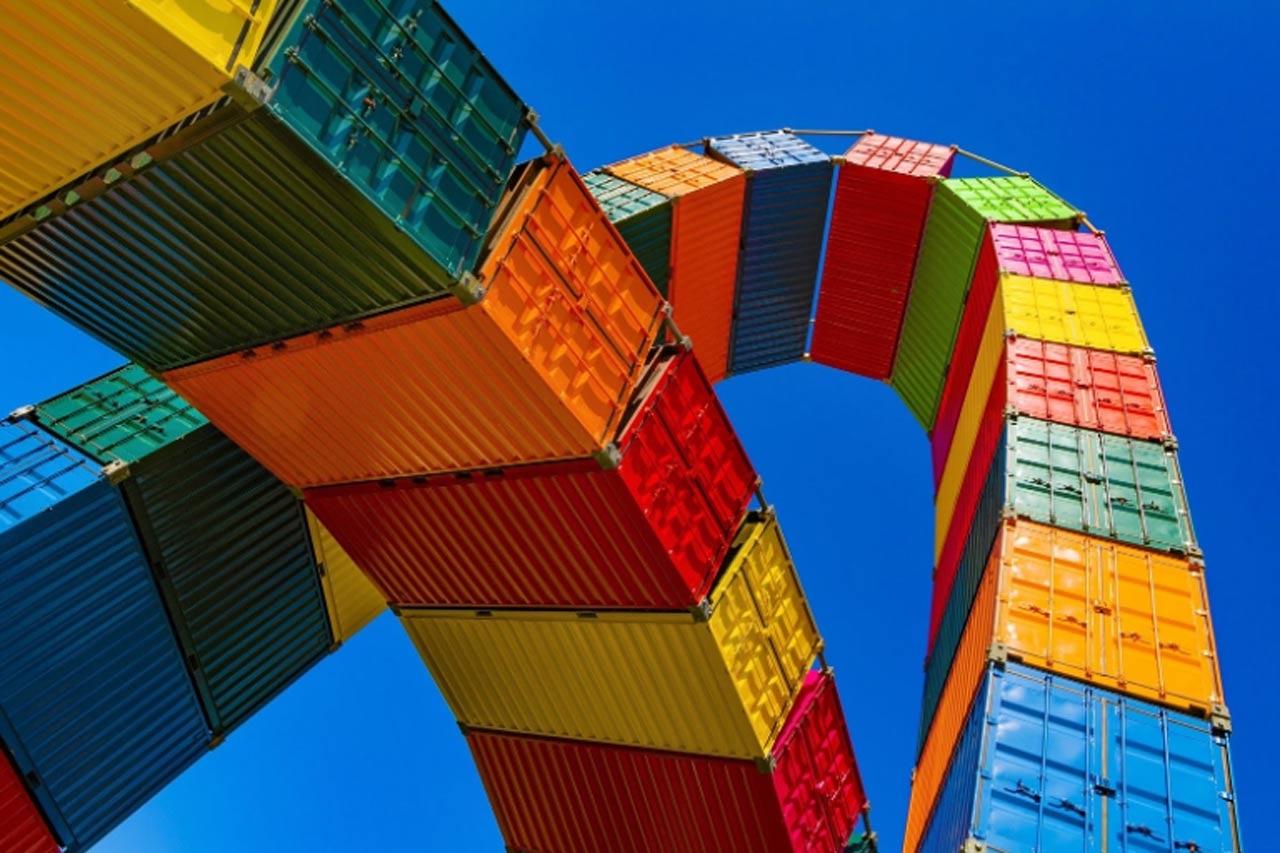
REVIEW YOUR SALES CONTRACTS AND CHECK YOUR SUPPLIER CERTIFICATIONS BEFORE STARTING YOUR ORDER
Times have changed tremendously in the past months, so before stepping into a partnership with any supplier, it is smart to review your sales contract. Make sure it includes clauses of protection in the event of errors or any regulation changes. Here also keep in mind the best method of payment for both parties is either a Letter of Credit or a 20% deposit. For AdvaCare certifications please check more about our extensive registration capabilities.CHECK MANUFACTURER CAPACITY AND LEAD TIMES
Because the demand for PPE products increased dramatically worldwide, manufacturers not only in China but around the world are overwhelmed. They have been working non-stop from the moment the government permitted factories to go to full operation, while still ensuring worker’s safety. However, the demand is so big, that many other businesses in China and abroad have changed their assembly line to PPE production. Still lead times, and capacities are limited. Thus, it is smart to discuss your selected partner's means, before wasting time on order discussions such as volume, price, delivery process, or payment methods. Consider AdvaCare’s current lead times for production vary but have been accelerated to just 7 days for some products – check with our Global Sales Department for more information.
Don't want to miss the next AdvaCare article?

Recommended Content
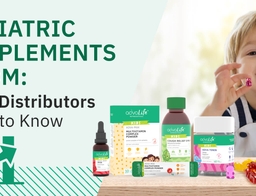
Shifting Trends in Child Wellness: How Savvy Distributors Can Leverage Changing Perceptions
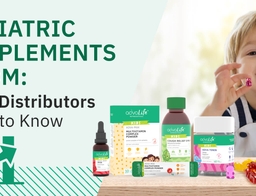
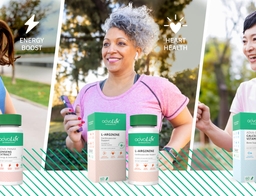
The Benefits of Supplements for Women
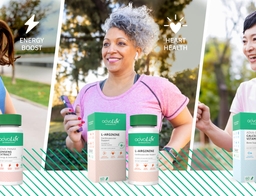
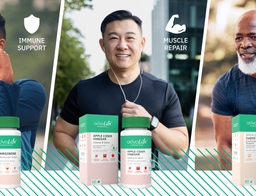
The Benefits of Dietary Supplements for Men
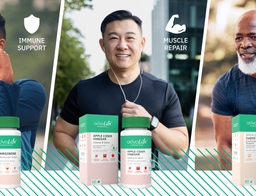